Turbojoe
Elite member
Your method of servo movement makes the most sense but I prefer to complicate things as much as humanly possible so I spent a bunch of time 3D printing and trying different versions until I was finally happy (and mentally exhausted). I didn't cut up the original plate. I just cut new pieces to fit from a sheet of 3/32" balsa. Everything fits together well. I even added a tab to my plate to lock everything in place. It's all just held together with rubber bands in the pictures for now. I still need to add the steerable nose gear and then I can start gluing things together. I already tucked a print into the bag for my 2nd Eaglet. For now it's just going in the Skylark.
Joe
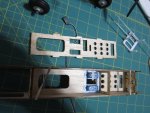
Joe
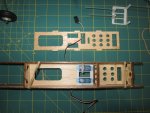
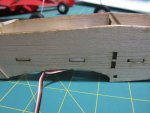
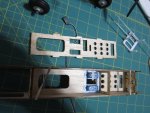